There are many kinds of industrial floor paints, and different types of epoxy floor paints have different performances; different floor conditions, performance and customer requirements require different floor paints, so customers should choose industrial sites according to what. What about the Ping variety? The following small series summarizes the following factors for selecting industrial flooring varieties for your reference:
1, health
Many modern industries, such as pharmaceuticals, cosmetics, food, beverages, chemicals and electronics, all have the same hygiene requirements. The manufacturing processes of these industries require a “clean room” working environment, such as the ground must be completely dust-free, without cracks. And right angle corners, easy to clean, and can meet other requirements, such as chemical resistance and mechanical wear resistance.
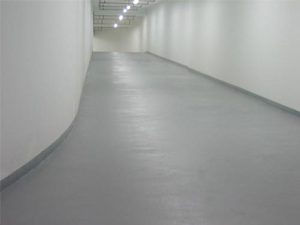
2, slip
The requirements of the pedestrian zone for the degree of slip resistance depend on the dry humidity of the environment. When considering the surface requirements of the ground, the slip resistance should be noted as possible. However, rough ground is difficult to meet cleaning and sanitation requirements, so the two must be balanced. Therefore, experts from China Epoxy Resin Industry Association recommend that the floor be designed according to different anti-slip requirements and meet other requirements.
3, impact / point load
Where the goods are often stored or transported in certain areas, such as production lines, warehouses, loading docks, etc., the floor must be designed to suit these specified working conditions. The movement of trucks, pallets, etc. with cargo will create a pressure load that is prone to damage if not reserved for local load design. It is also important to ensure that the stresses generated are not higher than the pressures of the entire flooring system material.
4, mechanical wear
Physical requirements such as impact resistance and mechanical wear are required for industrial floor design. Usually, the maximum wear occurs in the forklift passage or in certain areas where special treatment is required.
5, resistant to chemical corrosion
Not only the impact of the single chemical present in the plant on the ground, but also the potential chemical reactions should be considered, what if there is a chemical mixed on the ground? What is the strongest or most dilute concentration at the time of splashing or evaporation? High temperatures often increase the activity of chemicals – especially strong acids and bases. Temperature is also an important factor in some potential spill areas such as production, warehouse and shipping areas.
6, temperature
The drastic changes in temperature are the main cause of the failure of the traditional epoxy resin industrial floor. It is therefore very important to consider not only the temperature of the operating machine and the temperature of the product in the production process, but also the temperature in the adjacent area. Some activities are often carried out in certain areas, such as high pressure cooking, cooking, disinfection or freezing, and the temperature is often in an extreme state, so these areas require special treatment.
7, impervious
Today's environment requires that the ground coating must resist penetration to preserve the concrete and groundwater from dripping water and contaminants. Sometimes the impervious floor is only used to prevent the penetration of chemically corrosive liquid contaminants such as metal processing, galvanizing, food processing (dairy, meat, vegetables), and some chemicals when cleaned. Products such as: cleaning agents, steam and machinery.